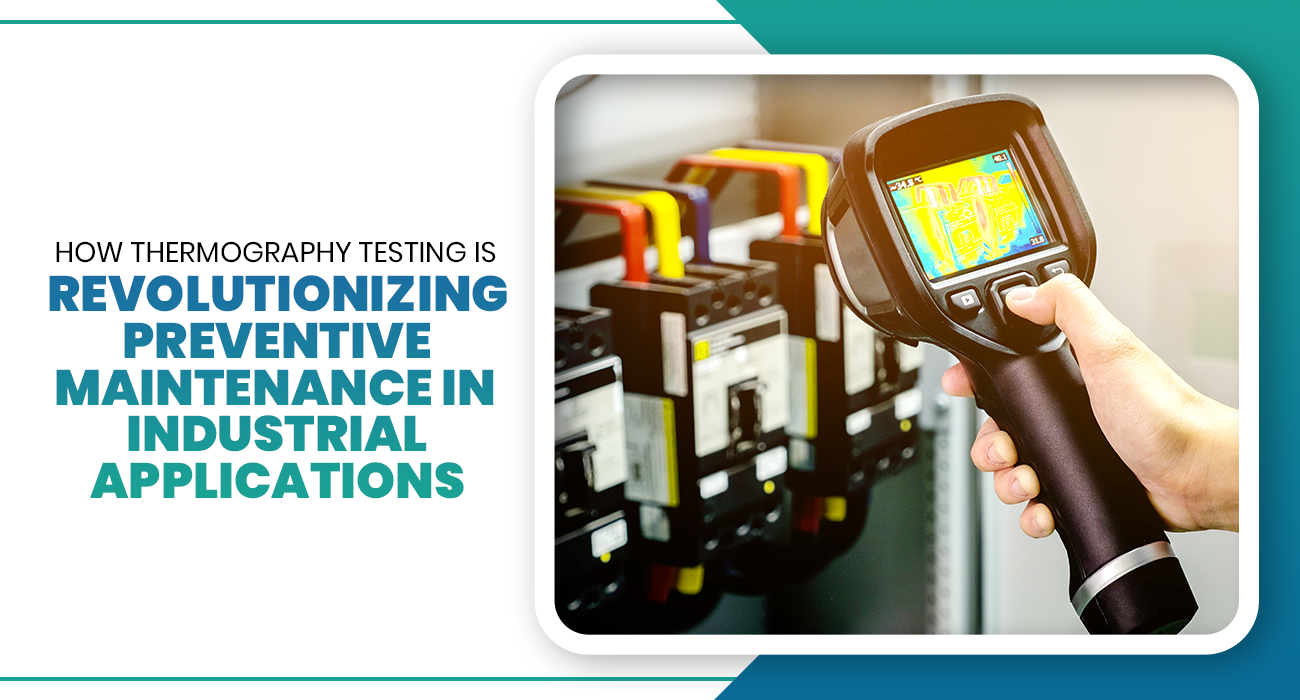
How Thermography Testing Is Revolutionizing Preventive Maintenance in Industrial Applications
In the industrial sector, maintaining equipment and machinery is crucial for minimizing downtime, ensuring safety, and increasing efficiency. One of the innovative technologies that have significantly contributed to this goal is thermography testing. This method uses infrared cameras to detect heat patterns and temperature changes in machines, electrical systems, and mechanical components, helping to spot potential issues before they cause failures. Let’s explore how thermography testing is revolutionizing preventive maintenance in industrial applications.
Early Detection of Problems
Thermography testing plays a vital role in the early detection of potential failures within industrial machinery.
- Monitoring Electrical Systems: Electrical components such as transformers, circuit breakers, and electrical panels often suffer from issues like overheating due to poor connections or overloading. Thermography testing helps in detecting these hotspots before they lead to equipment failure or fire hazards.
- Mechanical Inspections: Moving parts in machines and motors can develop faults such as misalignment, friction, or wear over time. Thermography testing detects these issues by capturing temperature differences, allowing for early maintenance interventions.
- Avoiding Unexpected Downtime: By identifying problems early, thermography testing minimizes the risk of sudden machine breakdowns, reducing unplanned downtime and costly repairs.
- Ensuring Safety: Early detection of overheating or potential electrical fires through thermography testing helps ensure a safer working environment for employees and reduces the risk of accidents.
Cost Efficiency
Implementing thermography testing as part of a preventive maintenance program can lead to substantial cost savings.
- Reducing Maintenance Costs: Detecting and resolving minor issues early through thermography testing prevents them from escalating into major, expensive repairs or replacements. This proactive approach saves money in the long run.
- Extending Equipment Lifespan: Regular thermography inspections can help maintain equipment in optimal working condition, reducing wear and tear and increasing the lifespan of machinery and components.
- Lower Energy Costs: Thermography testing also helps in identifying inefficient systems that may be consuming more energy than necessary. Addressing these inefficiencies can lead to significant energy savings, further lowering operational costs.
- Preventing Unexpected Downtime Costs: By identifying and fixing problems before they cause breakdowns, thermography testing avoids costly interruptions in production, making industrial operations more cost-effective.
Enhanced Predictive Maintenance
Thermography testing is an essential tool for predictive maintenance, which allows industries to plan for repairs and replacements at the right time.
- Timely Data for Decision Making: The data collected from thermography testing provides valuable insights into the condition of equipment. This enables maintenance teams to predict when a machine will likely fail, allowing them to schedule repairs during planned downtime rather than relying on reactive maintenance.
- Integrating with Other Predictive Tools: Thermography testing can be integrated with other predictive maintenance technologies, such as vibration analysis or ultrasonic testing, to provide a comprehensive view of machine health.
- Minimizing Disruptions: With thermography testing, industries can avoid sudden disruptions to production. This planning enhances workflow and helps avoid any unanticipated halts to operations.
- Optimizing Maintenance Schedules: With precise insights from thermography testing, maintenance teams can create more efficient and accurate maintenance schedules, reducing unnecessary interventions while ensuring timely repairs.
Improving Overall Efficiency
By incorporating thermography testing into preventive maintenance strategies, companies can improve their overall operational efficiency.
- Streamlining Inspections: Traditional inspection methods can be time-consuming and labor-intensive. Thermography testing, however, is quick and can scan large areas of machinery or electrical systems without causing any disruption to normal operations.
- Non-Destructive Testing: Thermography is a non-contact, non-invasive inspection method, meaning it does not interfere with machine performance or cause damage to equipment. This makes it ideal for continuous monitoring without impacting production.
- Comprehensive Coverage: Thermography testing can inspect areas that are otherwise difficult to access, ensuring comprehensive coverage of equipment and systems.
- Boosting Productivity: By reducing downtime, enhancing machine performance, and preventing failures, thermography testing ultimately leads to improved productivity and more efficient industrial operations.
Conclusion
Thermography testing has become an invaluable tool in the field of industrial preventive maintenance. Its ability to detect early signs of wear, electrical issues, and inefficiencies before they lead to costly failures has revolutionized the way industries maintain their equipment. With companies like Cornerstone Middle East integrating thermography testing into their preventive maintenance services, businesses can not only enhance their equipment’s longevity and safety but also improve cost-effectiveness and overall efficiency. By embracing this technology, industries are moving towards a future of smarter, safer, and more efficient operations.
Post a comment